Inicio / Servicios de fabricación / Servicio de fabricación de moldes / Servicio de fabricación de moldes de inyección
Fabricación de moldes de inyección de plástico
La fabricación de moldes de inyección de plástico es un proceso de precisión para fabricar moldes de inyección personalizados. First Mold ofrece soluciones globales de moldes de inyección de alta calidad con nuestro avanzado equipo de diseño de moldes.
- Disponible para utillajes rápidos y utillajes de producción.
- Utiliza equipos de marcas líderes como Haas, GF+ y Makino.
- Alcanza una precisión de ±0,0254 mm (±0,001″).
- Soluciones de moldes de inyección llave en mano
Si es necesario, podemos firmar un acuerdo de confidencialidad antes de facilitar el presupuesto.
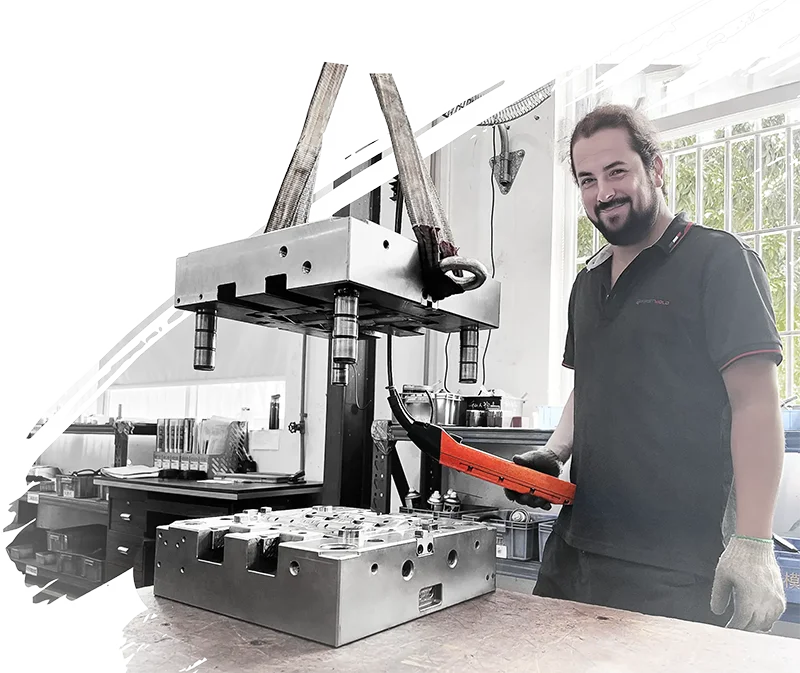
¿Qué es la fabricación de moldes de inyección?
La fabricación de moldes de inyección es un proceso de precisión que convierte materiales como el acero para herramientas, el acero preendurecido y las aleaciones de aluminio en moldes personalizados mediante técnicas especializadas de mecanizado y fabricación. En esencia, el objetivo es aprovechar las propiedades únicas de estos materiales para crear herramientas duraderas y repetibles capaces de producir piezas de plástico de alta precisión. Esto permite a los diseñadores de productos no sólo validar prototipos, sino también escalar a la producción en serie a escala de un millón de unidades.
Como paso fundamental del proceso de moldeo por inyección, la fabricación de moldes es un paso indispensable en la fabricación de piezas de plástico, ya que sirve de puente entre los conceptos de diseño y los productos tangibles de gran volumen.
Tipos de servicios de fabricación de moldes que ofrecemos
Los moldes de inyección que fabricamos pueden clasificarse en varias categorías en función de diferentes criterios:
Por frecuencia de uso:
- Herramientas rápidas
Diseñado para producciones rápidas de corto plazo, lo que permite crear prototipos y realizar pruebas con rapidez.
- Herramientas de producción
Aplicable para la fabricación a largo plazo de grandes volúmenes, lo que garantiza su durabilidad y estabilidad durante todo el proceso de producción.
Por material:
- Moldes de aluminio
Preferidas por su menor tiempo de mecanizado y su menor coste, son adecuadas para producciones de menor volumen.
- Moldes de acero
Para la producción de grandes volúmenes debido a su durabilidad y longevidad superiores.
- Moldes de cobre berilio
Se utiliza en partes específicas del molde que requieren propiedades únicas, como la conductividad térmica, en moldes aleados con cobre de berilio.
Por mecanismo de desmoldeo:
- Moldes de dos placas
El tipo más sencillo y común, en el que el molde se divide en dos mitades para expulsar la pieza.
- Moldes de tres placas
Más complejo, que permite el desmoldeo automático y la creación de piezas más complejas, con una placa adicional para la separación del sistema de correderas y compuertas.
Muchos clientes de todo el mundo han hecho fabricar diversos tipos de moldes en First Mold
"Como ingeniero de producto, necesitaba un socio que pudiera gestionar tanto moldes prototipo de bajo volumen como utillaje de producción de alto volumen. El equipo de First Mold suministró un molde de acero P20 multicavidad que redujo nuestro tiempo de desarrollo en 30%. Su experiencia en el moldeo de paredes finas para nuestros dispositivos IoT cambió las reglas del juego: se acabaron las marcas de hundimiento y los problemas de alabeo. Ahora estamos escalando a 500.000 unidades con cero defectos".
Alex Johnson
Ingeniero superior de producto
"La gestión de proyectos de automoción requiere moldes que sobrevivan a más de 500k ciclos. Los moldes de acero S136 endurecido de First Mold para nuestras carcasas de baterías de vehículos eléctricos superaron las expectativas. Incluso sugirieron un diseño de refrigeración conforme que redujo el tiempo de ciclo en 15%. Además, su documentación conforme a ISO aceleró nuestras auditorías de proveedores".
Sarah Thompson
Jefe de proyecto
Flujo de trabajo del servicio de fabricación de moldes
En First Mold, nuestro flujo de trabajo sistemático de fabricación de moldes garantiza soluciones de ingeniería de precisión, normalmente estructuradas en seis fases clave:
1. Análisis de productos y diseño de moldes
Basándose en la estructura del producto, el material y los requisitos del cliente, First Mold lleva a cabo un análisis de viabilidad y una evaluación de la viabilidad de fabricación (MFA). A continuación, nuestros diseñadores de moldes crean modelos CAD 3D detallados y planos técnicos de ingeniería 2D para todos los componentes del molde.
2. Selección del material del molde
Seleccionamos los materiales (por ejemplo, acero H13, S136, P20, aleaciones de aluminio, cobre berilio) en función del volumen de producción, la finalidad y el presupuesto. También se evalúan previamente los requisitos de tratamiento térmico del molde para mejorar su durabilidad y longevidad.
3. Mecanizado de moldes de precisión
Los componentes, como cavidades y núcleos, se someten a un proceso de desbaste, fresado de alta precisión y tratamiento de superficies. Los procesos incluyen fresado CNC, mecanizado por descarga eléctrica (EDM) y tecnología de corte por hilo de precisión.
5. Moldeo de prueba y optimización
Las pruebas se realizan en las máquinas de moldeo por inyección de alta precisión de First Mold. Se registran los parámetros, se analizan los defectos y se optimiza el molde para garantizar una producción perfecta y la consistencia de las piezas.
Soluciones para moldes de inyección Aplicaciones
El objetivo final del servicio de fabricación de moldes de inyección es la producción de piezas moldeadas por inyección. Los moldes producidos pueden ser utilizados por los clientes para su propia producción de moldeo por inyección o confiarse a fabricantes para la producción de moldeo por inyección.
Estos dos conjuntos de imágenes son moldes utilizados en la industria de bienes de consumo y moldes médicos en su aplicación final durante la producción.
Por qué destacamos
En la fabricación de moldes de inyección, una fábrica de moldes de inyección de calidad debe dar prioridad a la reducción de costes para sus clientes. En First Mold, comprendemos perfectamente este principio gracias a nuestra colaboración con los clientes. Mediante la aplicación de estrategias innovadoras para optimizar la eficacia de la producción y el uso de materiales, ayudamos sistemáticamente a nuestros clientes a reducir los gastos de fabricación. Este compromiso con la ingeniería de valor es precisamente la razón por la que hemos asegurado nuestra posición entre los 10 líderes del sector.
Capacidad de respuesta global de los servicios
Caso: Colaboración multinacional para una marca mundial de electrónica de consumo
Destacados:
Fábrica de China + Centro técnico de China + Fábrica de México colaboración lograda Tasa de error 0% en la ejecución de proyectos transfronterizos.
Asistencia multilingüe 7×24 redujo el tiempo medio de resolución de problemas de los clientes a <4 horas (media del sector: 12 horas).
Innovación tecnológica y aumento de la eficiencia
Caso: Optimización del molde de inyección de carcasas de radio para una marca mundial de electrodomésticos
Avances:
La tecnología patentada de diseño de los patines acorta la duración del ciclo de inyección pasa de 45 a 32 segundos (28,9% de mejora).
Reducción de la tasa de defectos de los productos de 3,2% a 0,8%salvando al cliente $800.000 anuales en costes de reelaboración.
Soluciones adaptadas al sector
Caso: Desarrollo de moldes de nuevos materiales ligeros para un fabricante de vehículos aéreos no tripulados (drones)
Innovaciones:
Reducción del peso del molde 40% utilizando materiales avanzados y estructuras compuestas, impulsando la eficiencia de la producción del cliente mediante 25%.
Mejora del rendimiento del producto 88% a 97%reduciendo las pérdidas anuales de chatarra en $350,000.
Entrega rápida
Caso: Producción en serie de emergencia de moldes de carcasas de baterías para un fabricante de vehículos de nueva energía
Resultados:
Ciclo de entrega reducido de De 90 a 55 días a través de diseño modular + ingeniería paralela.
Permitió al cliente lanzar productos 1,5 meses antes de lo previstoasegurando Crecimiento de la cuota de mercado de 8% en el primer trimestre de ventas.
Taller y departamento de fabricación de moldes de inyección
Técnicas avanzadas de fabricación de moldes y producción de componentes clave
Los centros CNC de 5 ejes realizan el mecanizado a nivel de micras (±0,005 mm) para bases de moldes y conjuntos de núcleo/cavidad.
Sistemas de mecanizado CNC multieje
Fresado, torneado y rectificado de precisión para geometrías complejas
Fresado a alta velocidad de acero P20/S136 |
Torneado duro (HRC62+) para componentes preendurecidos |
Rectificado de superficies con acabado <Ra0,2μm. |
EDM (Mecanizado por descarga eléctrica)
Creación de detalles intrincados mediante la erosión controlada por chispas
Electroerosión por penetración: Conformado de socavados y microranuras (tolerancia de 0,1 mm) |
Electroerosión por hilo: Corte de aceros templados (hasta HRC65) con una precisión de ±0,002 mm |
Sistemas automatizados de cambio de electrodos 24/7 |
Ingeniería integrada de superficies
Combinación de pulido, texturizado y revestimiento
Pulido espejo (norma SPI-A1) |
Texturas personalizadas (normas VDI 3400/VDA) |
Revestimientos de DLC/TiN resistentes al desgaste |
Técnicas avanzadas de fabricación de moldes y producción de componentes clave
Nuestros moldes de inyección se fabrican normalmente mediante procesos de mecanizado CNC o EDM (Mecanizado por Descarga Eléctrica). Los componentes fabricados para estos moldes incluyen:
- Producción de moldes base
- Fabricación de núcleos y cavidades
- Sistemas deslizantes y elevadores
- Insertos a medida y componentes calientes
- Pasador guía de molde de inyección
- Casquillo guía de molde de inyección
- Pasador eyector de molde de inyección
- Corredera de molde de inyección
- Sistema de refrigeración de moldes de inyección
Instalación estratégica en México: Aceleración de la fabricación de moldes para Norteamérica
Además de la base de China, nuestra planta de México en Silao está redefiniendo los estándares de la fabricación de moldes de inyección de plástico para el mercado norteamericano. Situada estratégicamente para minimizar los plazos de entrega y los costes logísticos, la planta se especializa en utillaje rápidouna solución revolucionaria para las empresas que buscan rapidez, precisión y rentabilidad.
¿Qué podemos hacer?
DFM
Análisis del flujo del molde
Diseño de moldes
Producción rápida de herramientas
Fabricación de moldes de gran volumen
Herramientas de moldeo por inserción
Soluciones de moldes multicavidad
Sistemas de moldes de canal caliente
Herramientas de aluminio
Texturizado
Acabado de superficies
Juicio por moho
Mantenimiento del moho
Reparación de moho
Renovación de moldes
Diseño de la puerta
Optimización de la línea de separación
Montaje de moldes
Plazos de entrega más cortos
Proximidad a los principales centros de fabricación de Estados Unidos y Canadá.
Costes más bajos
Reducción de los gastos de transporte y optimización de la eficacia de la producción.
Innovación rápida
Acelere su comercialización con moldes de alta calidad listos en un tiempo récord.
Capacidad escalable
Se aceptan tanto moldes de prototipo único como moldes de producción de gran volumen.
- Recomendado
PREGUNTAS FRECUENTES
¿Qué materiales se utilizan habitualmente en la fabricación de moldes de inyección?
Los moldes de inyección suelen fabricarse con los siguientes materiales, que se eligen en función de los requisitos de producción, la complejidad de la pieza y consideraciones de coste:
1. Acero para herramientas
P20: Acero preendurecido para producción de volumen medio (por ejemplo, bienes de consumo).
H13: Acero resistente al calor para plásticos de alta temperatura (por ejemplo, resinas de ingeniería).
S136/S-STAR: Acero resistente a la corrosión para moldes ópticos/médicos que requieren acabados de espejo.
2. Aluminio
7075/6061: Se utiliza para la creación rápida de prototipos o la producción de bajo volumen debido a su mecanizado más rápido y menor coste.
3. 3. Acero inoxidable
420/440C: Ideal para superficies muy brillantes o entornos corrosivos (por ejemplo, moldes de PVC).
4. Cobre berilio
Se utiliza para insertos en zonas de alta temperatura para mejorar la eficacia de la refrigeración.
5. Acero endurecido
NAK80/NAK55: Para moldes de alta precisión y larga duración (por ejemplo, automoción/electrónica).
¿Ofrece su fábrica servicios posventa o de mantenimiento para los moldes de inyección que produce?
Sí, los fabricantes de moldes reputados suelen ofrecer servicios completos de asistencia posventa y mantenimiento para garantizar el rendimiento del molde a largo plazo y la satisfacción del cliente. Esto es lo que puede esperar:
1. Período de garantía
Cobertura estándar: La mayoría de las fábricas ofrecen un 12-24 meses de garantía contra defectos de material o fabricación.
Alcance: Reparaciones o sustituciones gratuitas por problemas como desgaste prematuro, fugas en el sistema de refrigeración o errores de alineación.
2. Servicios de mantenimiento
Mantenimiento preventivo:
Inspecciones, limpieza y lubricación periódicas para prolongar la vida útil del molde.
Ejemplo: Sustitución de pasadores eyectores desgastados o pulido de cavidades para mantener el acabado superficial.
Reparaciones correctivas:
Reparación de daños por mal uso (por ejemplo, núcleos rotos, superficies arañadas).
Coste: Suele facturarse por horas o como tarifa plana post-garantía.
3. 3. Asistencia técnica
Solución de problemas: Guiado remoto para problemas como alabeo de piezas o destellos.
Optimización: Ajuste del tamaño de las compuertas o de los canales de refrigeración para mejorar los tiempos de ciclo.
4. Suministro de piezas de recambio
Disponibilidad: Las fábricas almacenan los componentes críticos (por ejemplo, insertos, deslizadores, calentadores).
Plazos de entrega: Piezas estándar enviadas dentro de 3-5 díasLas piezas personalizadas pueden tardar más.
5. Mejoras y modernizaciones
Mejoras materiales: Cambio a acero templado para plásticos de alta abrasión.
Integración de la automatización: Incorporación de la robótica para acelerar la expulsión de piezas.
¿Qué cualificaciones y certificaciones tiene su fábrica de moldes de inyección?
First Mold, como fábrica de moldes de inyección top 10, está plenamente acreditada con las normas internacionales de calidad y medio ambiente Contamos con la certificación ISO 9001 para la gestión de calidad e ISO 14001 para la gestión medioambiental También cumplimos con las normas específicas de la industria y nos sometemos a auditorías periódicas de terceros Estas certificaciones y cualificaciones sirven como prueba de nuestro compromiso de ofrecer soluciones de moldes de inyección precisas, fiables y de alta calidad
¿Cómo garantiza su fábrica que la calidad de los moldes de inyección cumple los requisitos del cliente?
Garantizamos la alta calidad de cada molde mediante un sistema integral de control de calidad y tecnologías líderes en el sector. Así es como lo hacemos:
1. Garantía de calidad en la fase de diseño
Simulación en primer lugar:
Utilizamos software como Moldflow y AutoForm para realizar análisis de flujo y simulación de estrés, prediciendo y optimizando de antemano aspectos como el llenado, el enfriamiento y la deformación.
Revisión del diseño para la fabricación (DFM):
Colaboramos con los clientes para optimizar el diseño de los productos, reduciendo posibles defectos (por ejemplo, grosor desigual de las paredes, marcas de hundimiento).
2. Control de materiales y procesos
Certificación de materiales:
Sólo utilizamos aceros para moldes con certificación ISO (por ejemplo, ASSAB, Buderus), con informes de material (dureza, composición) proporcionados para cada lote.
Mecanizado de precisión:
Utilizamos equipos de alta precisión como CNC de 5 ejes (precisión ±0,005 mm) y electroerosión por espejo (rugosidad superficial Ra<0,1μm).
3. Inspección de todo el proceso
Inspección durante el proceso:
Las dimensiones clave se comprueban con una MMC (máquina de medición por coordenadas) después de los pasos críticos (tolerancia ±0,01 mm).
Inspección de la calidad de la superficie:
La rugosidad de la superficie se mide mediante interferometría de luz blanca para garantizar Ra≤0,02μm (estándar de grado médico).
4. Pruebas y validación del moho
Grabación completa de parámetros:
Durante las pruebas, controlamos la presión de inyección, la temperatura y el tiempo de ciclo, generando informes para la aprobación del cliente.
Simulación de producción en serie:
Los moldes se someten a 5.000 ciclos continuos para verificar su vida útil y estabilidad (sin atascos ni deformaciones).
5. Certificación y normalización
Certificación del sistema:
Estamos certificados conforme a los sistemas de gestión de la calidad ISO 9001:2015 e IATF 16949 (industria automovilística).
Documentación rastreable:
Cada molde se suministra con documentación completa (planos de diseño, datos de inspección, registros de mantenimiento).
6. Seguimiento posventa
Garantía gratuita:
Ofrecemos una garantía de 12-24 meses que cubre los defectos de materiales y mano de obra.
Respuesta rápida:
Se proporciona asistencia técnica remota o in situ en 48 horas, con piezas de repuesto disponibles para reparaciones de emergencia en 72 horas.
¿Cuál es el plazo de entrega habitual de un proyecto de molde de inyección personalizado?
Nuestro calendario de entrega de moldes comienza en el momento en que usted confirma el pedido y nosotros iniciamos el diseño del molde, y se extiende hasta la primera fase de prueba.
Para la herramienta rápida, solemos completar el proceso en 7 días, mientras que para los moldes de producción, el plazo suele abarcar de 30 a 45 días. Dado que los moldes de producción requieren más tiempo para completarse, nuestro equipo mantendrá una estrecha comunicación con usted para garantizar que se cumplen sus requisitos.
Antes de la primera prueba oficial, realizamos pruebas internas. Además, realizaremos 2 ó 3 pruebas más para identificar y eliminar eficazmente los posibles defectos de moldeo por inyección que pudieran surgir durante la producción.
¿Qué ocurre si es necesario realizar modificaciones una vez iniciada la fabricación del molde de inyección?
Entendemos que pueden ser necesarios cambios incluso después de que comience la producción. Nuestro equipo evaluará rápidamente las modificaciones solicitadas y analizará el impacto en el coste y el calendario. A continuación, aplicará ajustes controlados para garantizar que el molde final mantenga su precisión y calidad, minimizando al mismo tiempo las interrupciones en el calendario de su proyecto.