在上一篇关于注塑模具制造设计 (DFM) 的文章中,我们探讨了以下方面的重要作用 DFM 之间 注塑模具 或成型工厂和客户。接下来,我们将深入探讨模具设计师的另一个强大工具:模流分析。模流分析是一种先进的模拟技术,与 DFM 原理相辅相成,使设计人员能够深入了解注塑成型过程中熔融塑料的行为。
什么是模流分析?
模流分析是一种利用 CAE 软件 (如 Moldflow、C-Mold、Z-Mold 等)对注塑进行有限元模拟、 保持压力塑料零件的冷却和翘曲过程。
模流分析可以有效预测模具在实际生产中可能遇到的问题,如填充不足、焊线和翘曲变形等,从而优化模具设计阶段,避免生产问题。此外,模流分析还能为优化模具设计和改进生产流程提供理论依据。
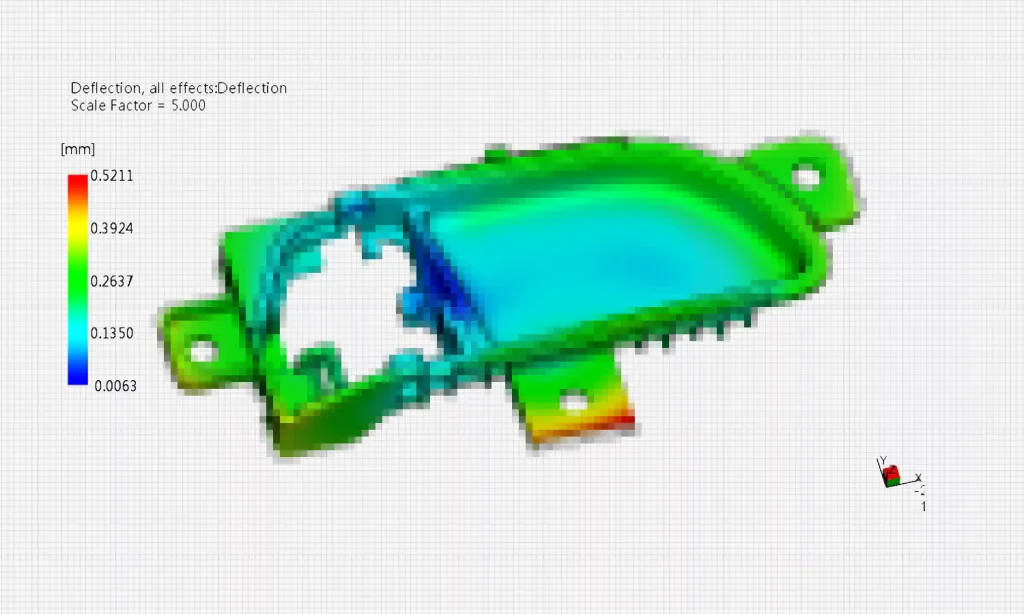
模流分析与 DFM 的关系
DFM(为制造而设计)是一种以制造为核心的设计方法,它要求在产品设计的早期阶段就考虑制造的可行性和成本效益。DFM 涵盖整个产品开发过程,包括概念设计、详细设计、流程规划和生产制造阶段。
在塑料产品制造领域(包括汽车、航空航天、医疗、设备、消费品、电子、个人护理和大多数其他行业),DFM 在模具设计中的应用同样至关重要。通过 DFM,设计师可以评估和优化产品设计,使其更易于制造。这包括评估可制造性、确定最佳制造方法,以及优化产品设计以降低制造难度和成本。
总之,模流分析和 DFM 都是汽车制造业模具设计和制造的重要工具。它们相辅相成,能有效提高模具质量和生产效率,同时降低生产成本。
模流分析的基本过程
I.网格生成
支持的文件格式
模流分析软件支持从主流 CAD 软件中读取 3D 文件格式,如 * * * * * *。.igs, *.stp, *.x_t*.prt、*.jt、*.catpart 以及有限元软件生成的其他网格格式,如 *.stl、*.bdf、*.nas。
网格质量控制
生成网格时,有必要控制网格质量以满足分析要求。
II.材料选择
材料类型
大多数模流分析软件的数据库中都有数千种材料供用户选择,包括热塑性塑料、热固性塑料、金属、冷却介质等。
材料模型
模流分析以聚合物流变学、传热学、结晶动力学和材料力学等理论科学为基础。材料特性模型是分析的基本输入数据。
在传统注塑成型中,常用的材料模型主要包括粘度模型、PVT 模型和结晶动力学模型,而比热容、热导率和机械性能等因素是影响模型的关键因素。
III.流程设置
目前,大多数模流分析软件的过程控制分为 CAE 模式和注塑机模式。
CAE 模式主要用于初步评估,不考虑注塑机的影响。注塑机模式主要用于后期验证,可根据实际注塑机的注塑方法设置工艺。
1.填充设置
(1) CAE 模式
A.填充时间
設定產品充填所需時間,並在分析過程中將其轉換為流速,作為求解的初始條件。创建新流程时,Moldex3D 会根据产品体积和成型材料自动推荐合适的充填时间。
B.多级
流速设置 对于结构复杂、流线较长的大型产品,通常采用分段注塑成型来实现均匀的流线速度。
C.多级压力设置
压力是指克服熔体流动阻力所需的压力,在实际成型中,是指注塑螺杆对熔体施加的压力。
D.V/P 切换
在产品填充阶段,通常通过注塑速度来控制流动前沿的推进。当产品即将完成充填时(95%~99% 容积),为防止因注入压力过大而造成过量充填和闪蒸,需要将控制方式从速度控制切换为压力控制。
(2) 注塑机模式
A.多级流速设置
注塑机模式允许用户使用实际生产工艺参数进行模拟分析,或向生产部门输出合适的工艺参数进行试生产。
B.多级压力设置
注塑机的压力是指螺杆对熔体施加的压力,为熔体的推进提供动力。
C.V/P 切换
大多数注塑机的 VP 控制器都会直接设置开关的切换位置。
2.包装设置
填料的目的是补偿空腔中在充填阶段未完全填满的熔体量,以及在充填阶段未完全填满的熔体量。 缩水 灌装后。包装参数设置通常包括包装压力和包装时间的分段曲线。
3.冷却设置
(1) 冷却时间
注塑成型的冷却时间主要取决于塑件的厚度,还与熔体温度、模具温度和模具钢的导热系数等因素有关。
常用的估计冷却时间的经验公式如下:
tc 是冷却时间,表示塑件厚度方向的平均温度冷却到顶出温度 TE 所需的时间;TM 是熔体成型温度;Tc 是模具温度;H 是塑件厚度;α 是塑料的热扩散系数。
(2) 冷却液设置
为了在冷却时间内消除每次塑料喷射所产生的热量,有必要估算出 冷却液 流量足以在固定时间内完成一定量的热交换。同时,为了获得更好的产品外观质量,有必要将模具表面温度的均匀分布控制在一定范围内。
IV.报告生成
由于模流分析以理论数值分析为基础,因此大部分输出结果都是数据值。为了便于结果解释和部门之间的交流,需要将结果以 PPT 报告的形式呈现。报告内容应包括产品信息、网孔信息、材料信息、工艺信息、结果解释等。
如何理解模流分析报告
现在,我们将回顾一份汽车零件的模流分析报告,就模流分析过程中需要考虑的关键方面提供有价值的见解。本案例研究将成为有效理解和解释模流分析报告的实用指南。
请注意,本案例中的图像已为某些保密目的进行了马赛克处理
基本信息
模流分析报告首先要提供必要的基本信息。其中包括项目编号、树脂材料、零件编号、模腔、日期和所用模流软件的具体版本(Mold Flow REV)等重要详细信息。此外,报告还包括进行分析的公司名称、负责研究的分析仪、模拟材料属性以及熔体温度、模具温度和填充控制设置等关键参数。
项目区域是另一项重要信息,有助于确定分析范围,并为评估结果提供背景。根据分析目标的不同,该区域可能包括整个部件,也可能集中在特定的关注区域。通过明确定义项目区域,模流分析报告可确保模拟结果准确反映预期条件。
报告中还记录了关键性能指标。其中包括最大注塑压力,表示完全填充模腔所需的压力。锁模吨位是另一个重要参数,表示锁模系统在注塑过程中保持模具闭合所施加的力。熔体前沿的最高和最低温度可帮助了解材料在填充过程中的热行为。
通过将这些细节纳入模流分析报告,利益相关者可以全面了解项目以及进行分析的具体条件。这种透明度可确保分析结果得到正确理解,并有效地用于模具制造过程中的决策。
材料数据
模流分析报告中的材料数据部分包括所分析树脂的重要信息。其中包括密度、模具温度、熔化温度和熔体流动指数。
网眼厚度诊断
网格厚度诊断是模流分析的一个重要方面。它包括评估分析中用于模拟零件和模具几何形状的网格元素的厚度。网格厚度诊断的目的是确保适当的网格细化程度,同时兼顾精度和计算效率。
分析师可以通过分析网格厚度来确定网格元素过厚或过薄的区域。元素过厚会导致结果不准确,而元素过薄则可能导致计算时间过长,甚至模拟失败。调整网格厚度有助于实现精度和计算效率之间的平衡。
这对于获得可靠的模流分析结果至关重要。它允许分析师在关键区域(如复杂几何形状或高流动或温度梯度区域)细化网格。通过优化网格厚度,模拟可以准确捕捉流动行为、压力分布、冷却特性以及影响注塑成型过程的其他重要因素。
初始闸门位置和尺寸
分析师会对各种因素进行评估,以确定最佳的闸门位置和大小。这些因素包括
填充模式:
制造商应选择浇口位置,以促进均衡、均匀的模腔填充。这可确保熔融塑料持续到达部件的所有区域,最大限度地减少潜在缺陷,如流动迟缓、焊缝或气孔。
压力和速度分布
浇口位置和尺寸会影响模具内的压力和速度分布。正确选择浇口有助于保持适当的压力分布,防止出现过大的压力下降或剪切应力,从而导致以下问题 零件翘曲和 沉痕.
冷却效率:
浇口位置应考虑零件的冷却要求。将浇口放置在能促进有效冷却的区域,有助于缩短生产周期和提高整体生产率。它还有助于最大限度地减少与热有关的潜在缺陷,如凹痕或零件变形。
成型性和可制造性
浇口位置和尺寸应符合模具的设计和制造限制。模具复杂性、模具限制和零件几何形状等因素都会影响浇口位置和尺寸的选择。目标是在成型性、零件质量和制造便利性之间取得平衡。
通过模流分析,分析师可以对不同的浇口位置和尺寸进行虚拟评估,模拟流动行为并评估对填充时间、压力分布、剪切速率和冷却效率等关键参数的影响。这种分析为在实际模具生产之前做出明智决策和优化浇口设计提供了宝贵的见解。
客户通常对模制件中浇口的位置和尺寸有特定的要求或偏好。这些规格可能基于所需的外观、功能或制造方面的考虑。在进行模流分析时,必须考虑这些客户指定的浇口位置和尺寸,以确保分析符合客户的期望。
填充时间
充模时间确实显示了熔体流动前沿的扩展,通常以阴影图的形式呈现。但是,关于使用云图的说法并不正确。充模时间通常不使用带等高线的云图显示。
在大多数模流分析中,充模时间确实是一个重要而关键的结果。它提供了有关熔体在整个模腔内流动行为的信息,有助于发现注塑成型过程中的潜在问题。
当熔体在基本相同的时间到达型腔的所有偏远部位时,就表明填充过程达到了平衡。这表明填充均匀,降低了成型部件出现缺陷或不一致的可能性。
充模时间结果有助于发现以下问题 短枪 和犹豫。当某一区域的材料填充不足时,就会出现短射,导致分析中出现灰色或不完整区域。相反,小区域内密集的轮廓线表示犹豫,表明可能存在流量中断或不一致,从而导致短射。
过度包装是另一个可以通过充模时间分析来识别的问题。如果在最初的型腔填充过程中,特定流道中存在过多熔体,则可能导致过度包装。过度包装会导致密度分布不均、产品重量超出预期、浪费材料,甚至造成翘曲问题。
喷嘴压力
在模流分析过程中,软件会计算和显示整个模腔的喷嘴压力分布。这些信息有助于评估填充行为、发现潜在问题并优化成型工艺。
在模流分析中分析喷嘴压力有几个目的:
填充行为:
喷嘴压力数据有助于了解熔体材料如何流动和填充模腔。它有助于深入了解流动前沿的进展、流动模式以及压力分布的任何变化。
部件质量:
通过分析喷嘴压力,可以评估其对部件质量的影响。喷嘴压力分布不均会导致填充不一致,如流量不平衡、焊缝或夹气,从而影响最终零件的性能。
闸门设计和尺寸:
喷嘴压力分析有助于评估闸门位置和尺寸的适用性。它有助于确定最佳的闸门尺寸,以确保适当的材料流动,并最大限度地减少潜在的问题,如高压下降或流动限制。
工艺优化:
喷嘴压力分析可确定潜在的工艺优化机会。它有助于调整注塑速度或熔体温度等工艺参数,使喷嘴压力分布更均匀,提高整体成型效率。
夹紧力的 XY 图
模流分析中锁模力的 XY 图显示锁模力随时间的变化。锁模力受充模平衡、保压和体积/压力控制过渡时间等因素的影响。即使对这些参数进行微小调整,也会导致锁模力发生显著变化。
确保最大锁模力不超过用于生产零件的注塑机的最大锁模力是至关重要的。超过机器的锁模力限制可能会导致潜在的设备损坏或影响零件质量。
通过分析锁模力 XY 图,制造商可以评估和优化模具设计和工艺参数,从而将锁模力保持在安全有效的范围内。这有助于确保成功可靠的注塑成型操作,防止对最终产品和注塑机本身造成任何不利影响。
空气疏水阀
当材料流从多个方向汇聚并被模腔内的气穴困住时,就会产生气阱。模流分析结果可准确识别并显示这些气阱。
当空气疏水阀位于模具的分模面上时,必须确保适当的气体排出,以防止残留的空气导致成型零件出现缺陷。为此,我们在存在空气疏水阀的模具设计中加入了排气槽或排气孔。
要消除气阱,就必须解决形成气穴的部位。修改产品壁厚、调整浇口位置和优化注塑时间都有助于缓解气阱问题,并提高整体零件质量。通过这些调整,可以优化材料流动,减少气穴的可能性,改善模腔的填充和密封。
焊接线
当两个熔体流动前沿汇合或一个流动前沿分离并重新组合时就会产生焊缝,这通常发生在熔体流过一个孔或遇到明显的流速变化时。在流速存在明显差异的情况下,也会形成焊缝,例如较厚的部分流速较快,而较薄的部分流速较慢,从而在两者的交界处形成焊缝。
焊缝可与充模时间、温度和压力图一起在模流分析中直观地显示出来。观察这些结果可以确定焊缝的存在和位置。减少注塑浇口数量以解决焊缝问题,有助于消除部分焊缝。此外,修改浇口位置或调整产品壁厚也可以改变焊缝的位置。
在注塑成型过程中,管理焊缝至关重要,因为焊缝会影响最终产品的强度和美观。通过优化模具设计和工艺参数,制造商可以最大限度地减少焊缝的出现和影响,从而生产出质量更高、更美观的注塑件。
塑料收缩量和收缩率估算
体积收缩收缩体积是指在注塑过程中由于保压而导致的零件体积的减少,有时也因翻译而称为收缩体积。通常用百分比表示。体积收缩率是一个中间结果,它显示了产品在保压和冷却阶段的收缩变化。不过,必须承认的是,顶出时的体积收缩被视为零件的最终体积缩减。
在实践中,一个特定的数据集会得出弹射时的体积收缩率。虽然收缩率应在整个模腔内均匀一致,但要达到完全一致却很困难。调整保压曲线有助于提高收缩率的均匀性,从而改善注塑件的整体质量。
偏转
冷却、收缩、分子取向和材料的其他机械特性等各种因素都会影响零件的挠度。
冷却因素导致的变形是指塑料材料在冷却和凝固阶段的变形。快速冷却会导致不同的冷却速度,造成不均匀收缩和潜在翘曲。
当材料从熔融状态转变为固态时,其固有的收缩会因收缩因素而导致变形。收缩会导致零件变形并造成尺寸变化。
在注塑成型过程中,当聚合物链沿特定方向排列时,分子取向会导致变形。这种分子排列会影响零件的机械性能和形状,从而导致变形。
整体挠度指的是零件的总变形量,考虑了所有的影响因素。相比之下,X、Y 和 Z 轴方向的挠度分量代表每个轴上的具体变形。
在模流分析中对零件变形进行分析时,考虑到所有这些因素对于确保精确预测和有效解决与翘曲或尺寸稳定性相关的任何潜在问题至关重要。
评估与反馈
模流分析评估通常涉及对与注塑成型工艺和零件质量有关的各种因素和潜在问题的全面审查。
模流分析中常见的一些评估项目包括
填充分析:
评估填充模式,确保完全填充模腔,不出现任何短射或流动犹豫。
冷却分析:
评估冷却效率,找出潜在的冷却相关问题,如热点、冷却不均匀或冷却时间过长。
挠度分析
分析因材料收缩、冷却或结构因素导致部件变形的可能性。
焊缝和空气疏水阀分析:
识别焊缝和空气疏水阀的存在,评估其对部件强度、外观和功能的潜在影响。
压力和温度分析:
评估注塑压力和熔体前沿温度,确保其在所选材料和工艺条件的可接受范围内。
夹紧力分析
验证计算出的在注塑过程中保持模具闭合所需的锁模力是否在注塑机的能力范围之内。
水槽痕迹分析:
确定因冷却不均匀或材料收缩而可能产生沉痕或表面凹陷的区域。
闸门位置分析:
评估浇口位置和尺寸,以优化填充模式,尽量减少焊缝,实现均衡填充。
物料流分析:
评估材料在整个模腔中的流动情况,确保填充均匀,避免出现喷射或流动不平衡等问题。
收缩和尺寸分析
分析材料收缩率,预测成型后零件的潜在尺寸变化。
这些示例仅涉及全面模流分析中评估标准的一小部分。具体的评估标准可能会根据项目要求、零件复杂程度和所需的质量标准而有所不同。
模流分析项目概要
上述内容是模流分析报告的完整概述。需要强调的是,模流分析报告中进行的数据分析会因分析的具体产品而异。一般来说,分析将包括以下几个方面:
填充分析:
- 填充时间
- 焊接线
- 空气疏水阀
- 流动前沿的温度
控股分析:
- 冻结层分数
- 注入位置的压力(XY 图)
- 体积收缩
- 水槽指数
- 夹紧力(XY 图)
挠度分析
- 部件的温度分布
- 部件内部的温差
结论
虽然我对模流分析持肯定态度,但在实际生产中,模流分析的实施往往会发现某些不足之处和意想不到的结果。有鉴于此,我决心深入探讨这一主题,并分享我个人对模流分析的见解、观点和看法。我是来自 FirstMold 的 Lee Young。在不久的将来,我将发布有关这一引人入胜的主题的内容,如果您也有类似的兴趣,我邀请您保持联系并关注我们。让我们一起探索复杂的模流分析,挖掘其在改进制造工艺方面的潜力。