包覆成型工艺 | 多材料精密制造
采用两步注塑成型技术,将硬质塑料与柔软耐用的覆盖层结合在一起。First Mold 的精密模具制造和高质量包胶生产在全球范围内得到了高度认可。
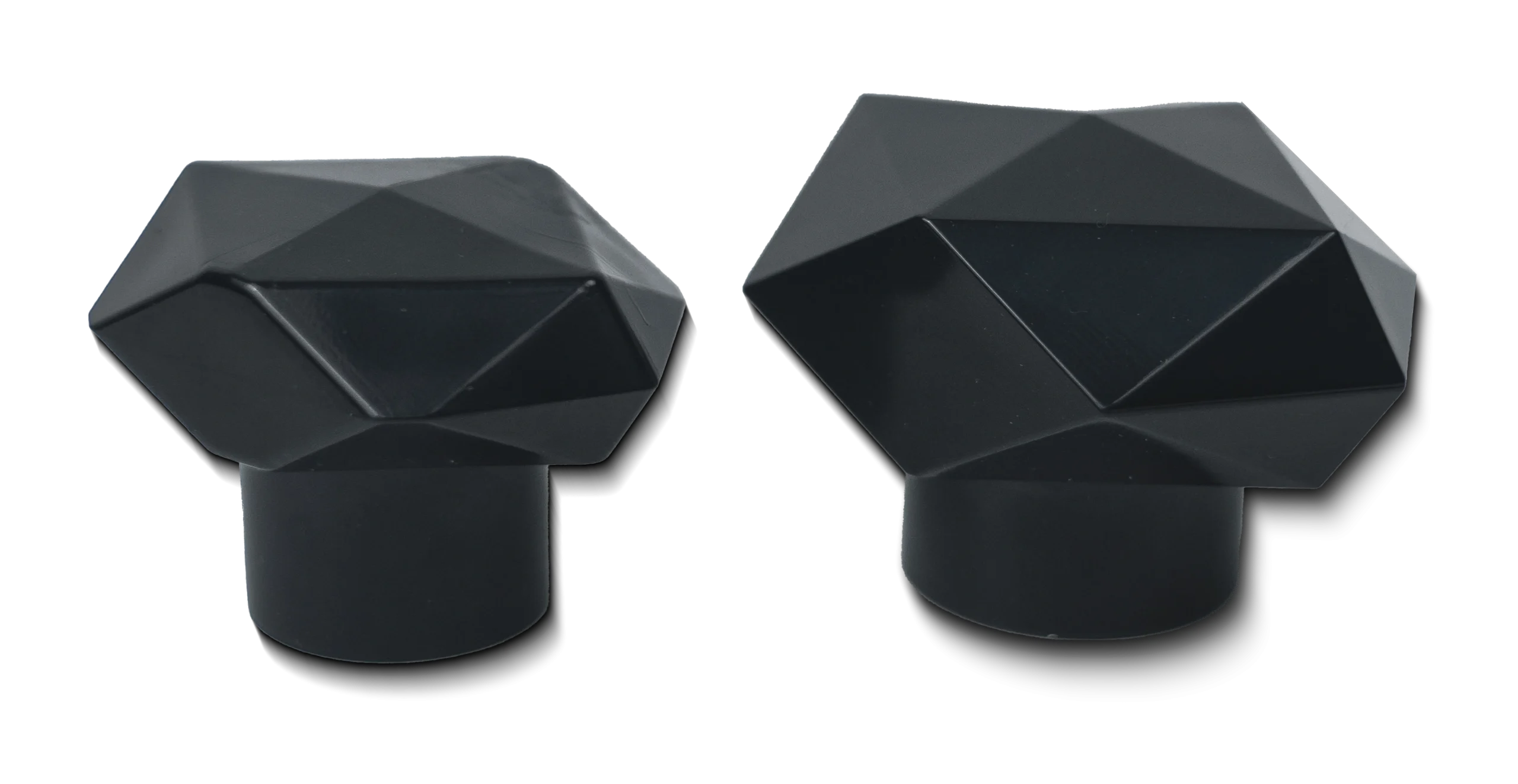
什么是包覆成型?
在产品设计中,有些产品可能会在基材(硬塑料或金属)外包裹一层软质材料(如 TPE、硅胶或橡胶)。这样做的目的是为了提高抓握力、防止滑动或美观。此类产品非常常见,如工具手柄、牙刷手柄和手机壳。其生产通常需要采用包覆成型工艺。
包覆成型是指使用两种不同的塑料材料,分别在一台注塑机中注塑成型。在一套模具中完成第一次注塑后,将产品取出并放入另一套模具中进行第二次注塑。因此,包覆成型通常需要两套模具。
不再有打滑的手柄 - 使用包覆成型进行粘合、密封和保护
First Mold 以其全面的能力在注塑成型行业处于领先地位。包胶成型是我们久经考验的专长之一。我们能解决棘手的包胶问题,例如
修复生产缺陷
- 分层:软质材料与硬质基材的附着力不足,容易剥落。
- 闪光:过多的材料会造成边缘粗糙,增加加工成本。
- 水槽痕迹不均匀的冷却会造成表面凹痕,破坏外观和耐用性。
- 材料实验室:测试 300 多对材料,提供兼容性报告。
- 精密模具:±0.5°C 的温度控制可消除闪蒸。
- 实时压力监控:自动调节压力,防止出现凹痕。
解决设计陷阱
- 壁厚不一致:过厚的硬质层会导致软质材料开裂;过薄的硬质层则缺乏强度。
- 明显的分割线:熔融塑料在关闭面溢出,破坏了优质产品的美观。
- 快速 DFM 审查:48 小时内获得壁厚提示。
- 获得专利的模具定位: <0.02mm error between base and overmold.
- 隐藏式分割线:电子/医疗设备的无缝解决方案。
行业 | 代表性产品 | 主要优势 |
医疗设备 | 手术器械手柄、假肢组件、导管连接器、注射器活塞 | 生物相容性(ISO 10993)、耐化学性、更符合灭菌要求(FDA/CE) |
汽车 | 方向盘手柄、安全气囊模块、轻质座椅外壳、电池组外壳 | 40-50% 重量减轻、减振(SAE J1475)、阻燃(UL94 V-0) |
消费电子产品 | 手机套、耳塞充电套、游戏手柄握把、智能手表带 | 防滑减震、IP68 防水、无缝多色美学设计 |
工业与工具 | 电动工具手柄、扳手防滑套、精密仪器外壳 | 300% 抗冲击性能提高,符合 MIL-STD-810G,符合人体工学,减少疲劳 |
包覆成型技术的材料组合
包覆成型技术是工业生产中多材料集成制造的典范,具有多种材料搭配选择。First Mold 将包覆成型的材料组合策略总结如下:
功能协同
即:将聚丙烯 (PP) 与 SEBS 弹性体相结合,利用分子链缠结消除粘合剂,同时实现医用手柄的抗伽马射线灭菌性(25kGy 剂量)。
提高性能
即:尼龙(PA66)-TPV 弹性体复合材料具有优异的耐油/酸腐蚀性和超低摩擦系数(μ=1.2)。它是电动汽车高压电池外壳的理想材料。
可持续创新
即:生物基 TPE 与聚乳酸(PLA)基材融合,提供完全可生物降解的解决方案。50% 可减少碳排放量,这意味着它符合 EN 13432 工业堆肥要求,是生态包装系统的革命性产品。
基质 | 包覆 | 典型应用 | 认证标准 |
聚丙烯 | TPE/SEBS | 医用手柄、工具手柄 | ISO 10993、FDA 21 CFR |
ABS | 热塑性聚氨酯 | 手机壳、智能手表带 | IEC 60529、RoHS |
个人电脑 | 液态硅橡胶(LSR) | 汽车透明纽扣、婴儿奶嘴 | IATF 16949、LFGB |
尼龙(PA6/PA66) | 冠捷 | 汽车电池外壳、工业齿轮 | UL94 V-0,MIL-STD-810G |
PBT | 玻璃纤维增强 TPE | 电动工具手柄、连接器 | EN 61340、IEC 60695 |
PEEK | 氟橡胶(FKM) | 航空航天传感器、医疗植入物 | ISO 13485、AS9100 |
金属嵌件 | TPE/TPU | 电动工具手柄、医疗器械 | ISO 2768、ASTM D638 |
POM | 热塑性弹性体(TPE) | 齿轮减震套筒、精密仪器外壳 | DIN 54800 |
PPS | 硅橡胶(VMQ) | 高温传感器、发动机部件 | SAE J2460、AMS 3217 |
PLA | 生物基 TPE | 环保包装、可生物降解的产品 | EN 13432、ASTM D6400 |
包覆成型与嵌入成型嵌入成型与双色成型双色模塑
包覆成型是将一种材料注入到现有的基底(如硬塑料或金属)上。这一过程分步骤完成,以形成保护层或功能层。在嵌件成型中,金属或电子元件等嵌件首先被放入注塑模具中。然后注入塑料以固定和整合嵌件。在两次注塑中,使用旋转模具在同一周期内注入两种不同的材料。
尺寸 | 包覆成型 | 插入成型 | 双色模塑 |
流程步骤 | 两步注塑硬模芯 → 软包覆 | 预插入 → 一次封装 | 双射注塑(旋转/滑动模具) |
材料组合 | 软硬结合(如 PP+TPE) | 塑料+金属/插件(如 PA66+铜) | 双色塑料(如 ABS+PC) |
设备要求 | 标准机器 + 兼容模具 | 标准机器 + 机器人/手动刀片放置 | 专用双色机 + 旋转模具(±0.02 毫米) |
材料互动 | 化学键(热力学兼容性) | 机械锁定(无化学键连接) | 物理分层(熔点同步) |
结构差异 | 分层封装(功能集成) | 插入式芯材(复合材料加固) | 无缝分层(美学融合) |
模具成本 | $$ | $ | $$$ |
生产周期 | 30-60 秒(两层之间需要冷却) | 45-90 秒(手动插入) | 20-40 秒(自动双拍) |
典型产品 | 工具手柄、医疗器械 | 汽车连接器、医用电极 | 双色尾灯、半透明键盘按键 |
常见问题
如何确定我的产品是否适合包覆成型?需要提前提供哪些关键参数?
我们建议提供以下三类参数供评估:
1.材料兼容性:
硬质基材(如 ABS/PC)和软质材料(如 TPE/TPU)的极性参数。
熔点差(ΔT≤50°C 为佳)。
如果没有数据,我们可以进行材料库匹配测试。
2.结构可行性:
刚性部件的厚度必须≥1.2 毫米,以承受二次成型压力。
在软质材料覆盖区域应预留 0.3-0.5 毫米的间隙,以防止注塑闪蒸。
3.功能要求:
标记防滑、密封或减震应用的受力点。
例如医用手柄的抓握区域需要更强的粘接强度。
First Mold 如何在小批量包覆成型生产过程中快速解决分层问题?
我们的 48 小时闭环承诺:
根源分析:
- 如果接口处没有熔化痕迹 → 设计缺陷(增加卡接特征或暗槽)
- 如果熔化层不完整 → 工艺缺陷(将软质材料的注射温度调整到硬质材料的 Tg +15℃)。
解决方案
三个优化包:材料替代/表面处理/结构升级
(例如:TPE-V 自粘合材料无需预处理)
成本保证:
- 100% 材料成本覆盖因我们的工艺错误而造成的返工。
First Mold 如何对耳机部件等微小的注塑产品进行精确控制?
我们拥有丰富的微精密制造经验,通过三种关键方法保持微米级精度:
1.模具制作
- 超平滑火花侵蚀(Ra≤0.02μm)
- 高精度 5 轴切割
- 密封面间隙 ≤0.005mm
2.过程控制
- 稳定的注入压力(≤1% 变化)
- 精确的温度控制(±0.5℃)。
3.检查
3D 激光扫描仪(精度 ±5μm)
X 射线 CT 扫描
检测小至 0.1mm³ 的气泡
对于突然增加的订单,贵公司生产能力的灵活性如何(仅限于包覆成型)?
我们通过 3 个核心战略来确保灵活的产能扩张,以应对过度成型订单的激增:
1.设备冗余和快速启动机制
- 专用设备库:
12 台包覆成型专用注塑机(锁模力 180-2500T),4 台战略储备机(总计 33%)处于备用状态。 - 快速转换能力
通过预热热流道和标准化模座接口,≤45 分钟完成模具切换(行业平均时间:2 小时)。
2.深度供应链整合
- 战略性原材料库存:
高频材料组合(TPE-PP、TPU-ABS)的 3 个月安全库存(≈500MT)。 - 供应商优先响应:
与 Covestro 和 ExxonMobil 签订的 VMI 协议可确保 72 小时内交付关键材料(TPE、LSR)。
3.动态容量分配和智能调度
- 人工智能容量预测系统
利用历史数据和实时负载分析调整生产计划。例如 - 在预测 50% 医疗处理订单增加前 2 周预先分配备用容量
- 在 ≤4 小时内自动优先处理紧急订单
- 轮班灵活:
从两班制无缝过渡到三班制,日产量增加 50%(10 万套→15 万套)。
如何在小批量试生产中以最低成本验证包覆成型工艺的可行性?
我们提供三阶段验证解决方案:
- 3D 打印原型: 采用硬树脂+软硅橡胶成型,单件成本小于 50 元,验证组装和触感体验。
- 软模试制: 带铝框架的耐高温 PEI 模具,成本仅为钢制模具的 20%,最多可生产 500 件。
- 模架重复使用: 如果已有镶件模具,则可增加软橡胶型腔,以节省 30% 的模具开发成本。
如何确保多材料包覆成型产品的准确配色? 采用什么色差标准?
我们采用两步色彩控制系统:准备
使用精密仪器根据潘通指南配色材料,创建颜色公式(最大 1.5 色差)。
实时检查:在制作过程中使用摄像系统即时监控和调整色彩。
质量标准:遵循 ISO 标准--批次内色差小于 0.8,批次间色差小于 1.2。